From scraps to new fibers

Some products are marked with a special Designed for circularity tag. They have received the tag since they meet the criteria below.
- At least 25 percent of the main material of the product is regenerated from cutting waste or other leftover materials from the manufacturing of Marimekko's products.
- The cutting waste and other leftover material from the production will be used as raw materials for future products.
- The product is made with monomaterials, which improves the recyclability of the product at end-of-use.
Closed loop is a circular economy operating model where materials used in products circulate back into the production of new products. The goal is to reduce natural resource consumption and production-related emissions. Marimekko has launched several initiatives to significantly reduce emissions throughout its entire value chain. The materials used in the products are key in this effort. We are particularly looking for materials whose production consumes fewer natural resources and supports our climate goals.
Together with its partners, Marimekko has put the closed-loop production model to the test by using cutting waste and other leftover materials from the manufacturing of Marimekko’s jersey products as raw materials for new products. In Marimekko's first closed-loop products, which will be available for sale in the summer of 2023, the share of recycled fiber is 25 percent and virgin cotton fiber is 75 percent to ensure durability and quality.
Our first closed-loop products were produced in Portugal. There are typically many different parties involved in closed-loop production, and that’s why an efficient process and close local cooperation are essential. Marimekko's closed-loop T-shirts, sweatshirts, and hoodies demonstrate the various stages of closed-loop production.
Testing digital product passport
We are piloting a digital product passport (DPP) with Erna closed-loop T-shirt, coming for sale during spring 2024. By scanning a QR code in the product's care label, the customers can access information on the sustainability of the product.
Digital product passports are designed to support circularity by giving access to product-specific information that enables, for example, product repair and recycling. They also increase the transparency of the value chain by opening different steps in the chain.
As a part of the Trace4Value research project, the pilot provides Marimekko with valuable experience in identifying the data needed for a digital product passport. In addition, it supports us in preparing for the DPP requirements, which are a part of the EU eco-design legislation for sustainable products coming into force by 2030.
Material collection and sorting
The Pedrosa & Rodrigues factory, which manufactures Marimekko’s jersey items, collects and sorts waste material generated during Marimekko product production based on color and material quality, allowing the original color to be used in the design. The color of our SS23 pilot project T-shirt, for example, is derived directly from the collected fiber.
Pedrosa & Rodriguez, S.A.
Rua dos Escuteiros nº42 | Gilmonde
4755-230 Barcelos | Portugal
From waste material to fiber
A fiber opening line is used at the Sasian factory to break down waste material into fiber. Marimekko uses either its own waste material generated during production or material from other brands' products, depending on the overall situation. The raw material for the SS23 pilot comes from Marimekko's jersey product manufacturing. The fiber opening line has seven cylinders with cutting blades that allow textile buttons and zippers to be removed. The textile waste has been transformed into fiber fluff after processing. The fiber is packaged into fiber bales before being delivered to a yarn manufacturer.
Sasia Rua Escola da Portela nº 50 | Apt. 7001
4761-908 Ribeirão | Portugal
From fiber to yarn
Yarn manufacturer Inovafil combines recycled fiber with cotton fiber to create a more durable material. The fiber material is then spun into yarn and delivered to the knitting factory. Recycled fiber accounts for 25% of the material in Marimekko's first closed-loop products, with virgin cotton fiber accounting for the remaining 75%. Our goal is to increase the proportion of recycled fiber in our products while maintaining product durability.
Inovafil
Rua Comendador Manuel Gonçalves | São
Cosme
4770-578 Famalicão | Portugal
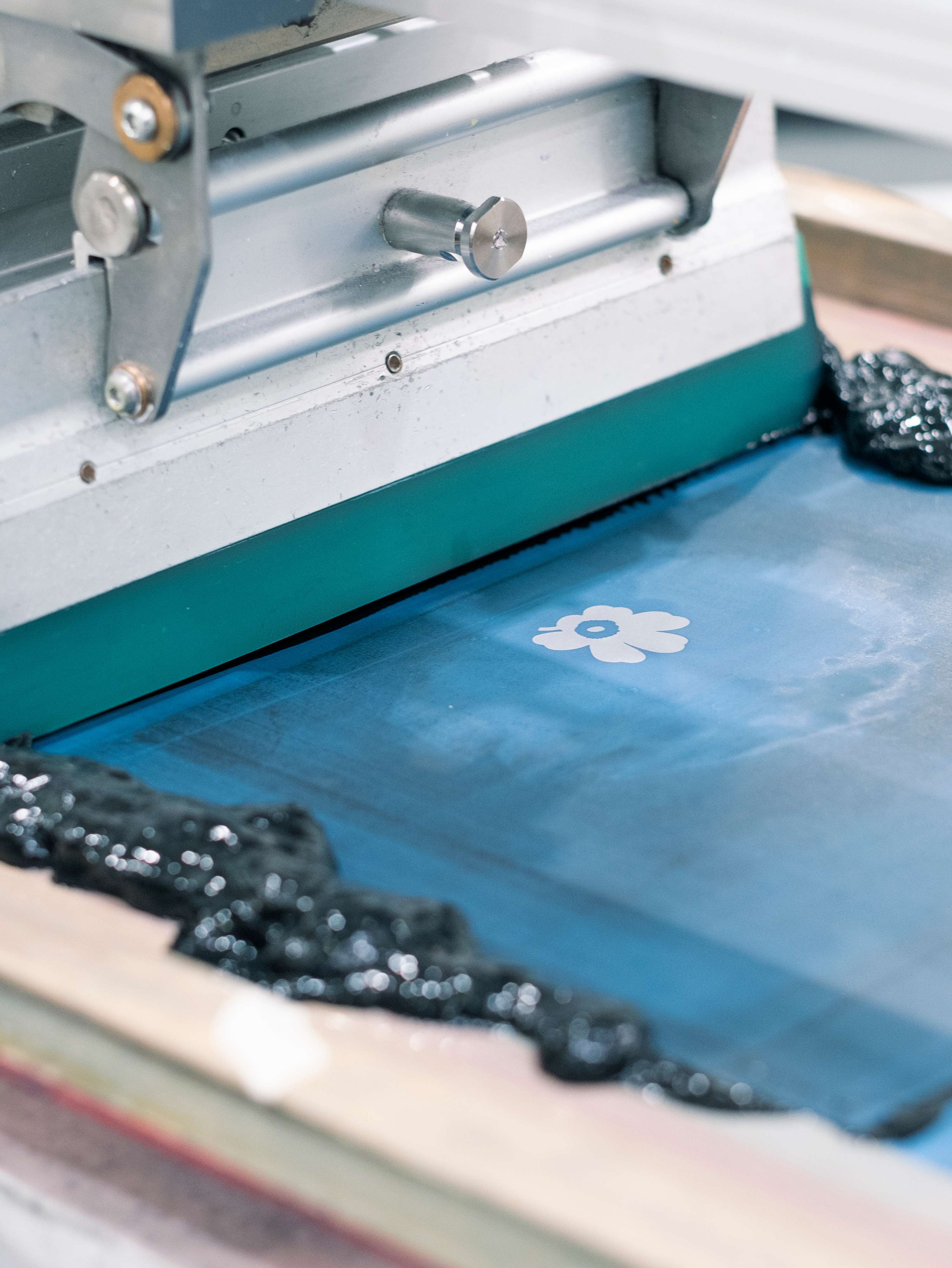
From yarn to fabric
Fabric manufacturer Trimalhas knits the yarn into a jersey fabric, which is then sent for finishing. The fabric is finished and washed at the Acatel factory. Following that, the fabric is returned to the Pedrosa factory to be cut into pieces in accordance with the sewing patterns.
Trimalhas Knit Inspiration, S.A.
Rua Eng. Orlando Vital Marques Rodrigues
Cardoso S. Tiago | 4835-244 Guimarães | Portugal
Acatel - Acabamentos Texteis, SA.
Rua do Barreiro, Nº. 310 | Gilmonde
4754-909 Barcelos | Portugal
From fabric to printed garment
The Cor Suspensa printing house prints the desired placement print onto the cut fabric pieces. The pieces are then delivered to the Cardacao de Cardoso & Santos garment factory, where they are sewn together to create the final product.
Cor Suspensa , Estampargem, LDA
R. D. Elvira Gomes Barroso, nº 2681
4755 - 230 Gilmonde | Barcelos | Portugal
Cardação de Cardoso & Santos, LDA
Rua das Calçadas, Nº. 450 | 4750 - 572 Mariz
Barcelos | Portugal
Marimekko's closed loop pilot project partners:
Jersey cutting, scrap collection and sorting
PEDROSA & RODRIGUES, S.A.
Recycled cotton production
SASIA
Yarn manufacturing
INOVAFIL
Fabric manufacturing
TRIMALHAS KNIT INSPIRATION, S.A.
Fabric finishing
ACATEL - ACABAMENTOS TEXTEIS, S.A.
Fabric cutting
PEDROSA & RODRIGUES, S.A.
Printing
COR SUSPENSA, ESTAMPARGEM, LDA
Sewing
CARDAÇÃO DE CARDOSO & SANTOS, LDA
Finishing and control
PEDROSA & RODRIGUES, S.A.